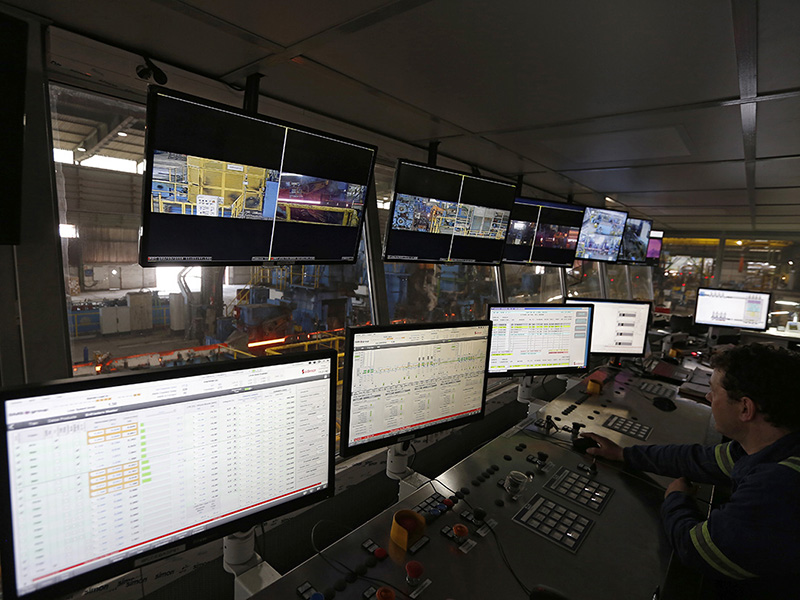
Tras su inauguración hace apenas unos meses, el nuevo Tren de laminación ha cumplido las exigentes expectativas de Sidenor tanto a nivel de productividad como de calidad de producto
¿Cuál es la clave del éxito para que una gran inversión cumpla con los resultados esperados en tan poco tiempo?
Desde Sidenor la idea era clara desde el inicio: apostar por la tecnología más puntera del mercado, poner el foco en la Industria 4.0 y contar con un equipo de profesionales que lo hacen realidad. Esta inclusión de tecnologías novedosas en la instalación, tiene como objetivo aportar valor al producto y detectar en tiempo real cualquier irregularidad en el proceso, de forma que nuestros productos lleguen al cliente habiendo cumplido rigurosos controles de calidad que garanticen las condiciones exigidas de cada pedido.
Para introducir estas mejoras tecnológicas, se han reformado tanto el Horno como la sistemática de carga del mismo. En el nuevo tren, para realizar una correcta carga del horno, se dispone de un sistema de Visión Artificial que lee la identificación de nuestras palanquillas y coteja la lectura versus el orden de carga establecido por el equipo de planificación. Se trata de un sistema de control anti mezclas de altísima fiabilidad.
Al horno se le ha dotado de cámaras de control, así como de sensores que permiten determinar la temperatura de las palanquillas en tiempo real. Con todos los datos que se registran, en el horno, se establece el óptimo calentamiento en función del material cargado para asegurar las características tanto mecánicas como la temperatura de salida adecuada asegurando que entren dentro de las especificaciones y garantías de calidad exigidas. El sistema de optimización posee un Módulo de Simulación que puede prever el comportamiento del material, obteniendo en dicha simulación la curva y temperaturas a las cuales se debería calentar. Este trabajo previo supone una mejora en cuanto a la gestión de energía consumida en cada carga.
Además del seguimiento visual de las cámaras, se han instalado sensores de última generación en los distintos elementos del tren para establecer un conjunto parametrizado de recogida de datos que permita conocer el estado de cada orden de producción en el mismo momento de la consulta. Con este seguimiento se tiene la situación de la palanquilla en cada parte del tren pudiendo consultarse en tiempo real los datos productivos asociados a la misma. El siguiente paso será en los próximos meses almacenar esos datos en una plataforma Big Data, desarrollada por Sidenor dentro de su proyecto Smart Factory incluido en la convocatoria HAZITEK 2017 como Proyecto Estratégico Singular. El objetivo general de este proyecto es conseguir implantar el paradigma de la fabricación inteligente en el proceso siderúrgico, consiguiendo la gestión integral del mismo y posibilitando la obtención de “aceros premium”, mediante la incorporación de inteligencia artificial y análisis big data en medios y sistemas de producción.
En un futuro cercano, se implantará un sistema de trazabilidad barra a barra que permitirá identificar unívocamente la trazabilidad del producto desde el origen, en Acería, hasta la salida en nuestras instalaciones acabadoras. Mediante el sistema Big Data y el análisis masivo de los datos se implementarán alarmas que ayuden en tiempo real a estabilizar y garantizar los procesos.