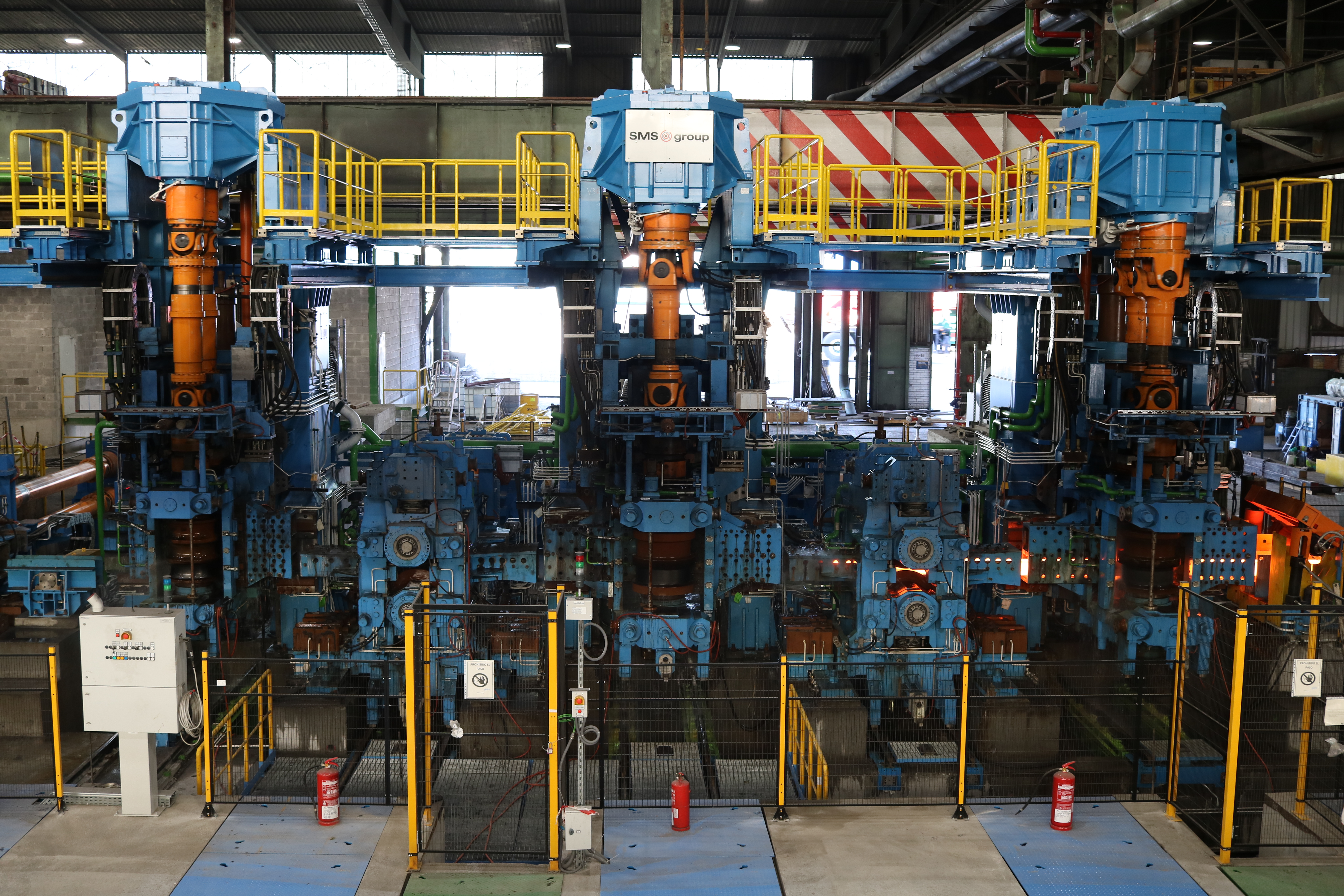
La Unión Europea es el segundo mayor productor de acero del mundo, pero desde hace años se enfrenta a diversas amenazas: una importante pérdida de capacidad productiva en relación al resto del mundo y sobre todo en relación a China, la necesidad de ser cada vez más competitivo en costes para garantizar la viabilidad de la cadena de producción de automóviles y de la industria metal mecánica europea y finalmente a compensar de alguna forma los incrementos de costes debido a la mayor exigencia europea en temas medioambientales y energéticos.
Para hacer frente a este complejo escenario, Sidenor Aceros Especiales S.L., como líder europeo en la producción de productos largos en acero especial, ha decidido llevar a cabo un proyecto con el que busca desarrollar nuevos productos que presenten un alto valor añadido, partiendo de una amplia gama dimensional de barras laminadas de alta calidad superficial e interna.
La consecución de este ambicioso objetivo ha sido posible gracias a la renovación del tren de laminación de la Planta de Basauri, que cuenta con un nuevo horno de recalentamiento más eficiente y un tren adaptado a un formato de palanquilla mayor.
Una parte fundamental de la apuesta de Sidenor consiste en aumentar las dimensiones geométricas de la palanquilla de colada continua hasta un formato cuadrado de 240 mm (frente a los 185 mm actuales). De esta manera, durante el proceso de laminación, la reducción final aplicada al material es mayor, lo que mejora significativamente tanto la calidad superficial como la interna del producto laminado.
En cuanto al horno de recalentamiento, la nueva instalación está basada en la tecnología de vigas galopantes, por la cual la distribución de temperaturas dentro del horno es más homogénea, permitiendo así optimizar las curvas de calentamiento con el objetivo de conseguir una mejora de la calidad así como un mayor rendimiento energético.
La adaptación del tren de laminación a palanquilla de 240 ha supuesto la instalación de un nuevo desbaste continuo, formado por 6 cajas H-V donde se alcanza una reducción media del 20%. Asimismo, se han añadido 2 cajas nuevas (H-V) al inicio del tren continuo para procesar el material desbastado con tolerancias mejoradas, además de otros elementos auxiliares que contribuyen a la obtención de un producto de alta calidad. Una vez más, la eficiencia energética es protagonista en el tren de laminación, ya que ha sido diseñado con el objetivo de reducir las pérdidas de temperatura entre cabeza y cola de las palanquillas y a lo largo del tren.
El nuevo tren de laminación cuenta con la tecnología más puntera del mercado, y gracias a ello, supone una de las bases sobre las que se asienta el concepto “innobars by Sidenor”. La aplicación del conocimiento adquirido por los más de 30 años de experiencia de Sidenor I+D en el desarrollo de productos y procesos sostenibles, la fabricación en las instalaciones más modernas y la utilización de las últimas posibilidades de la industria 4.0 completan los pilares de esta marca, dando solución a las necesidades más exigentes de nuestros clientes y cumpliendo ampliamente sus expectativas de valor. Este aspecto cobra especial importancia en lo concerniente al sector automoción, ya que actualmente se enfrenta a la necesidad de desarrollar componentes cada vez más complejos y de mayores prestaciones a un menor coste; siendo este mercado el 70% de la producción de Sidenor.