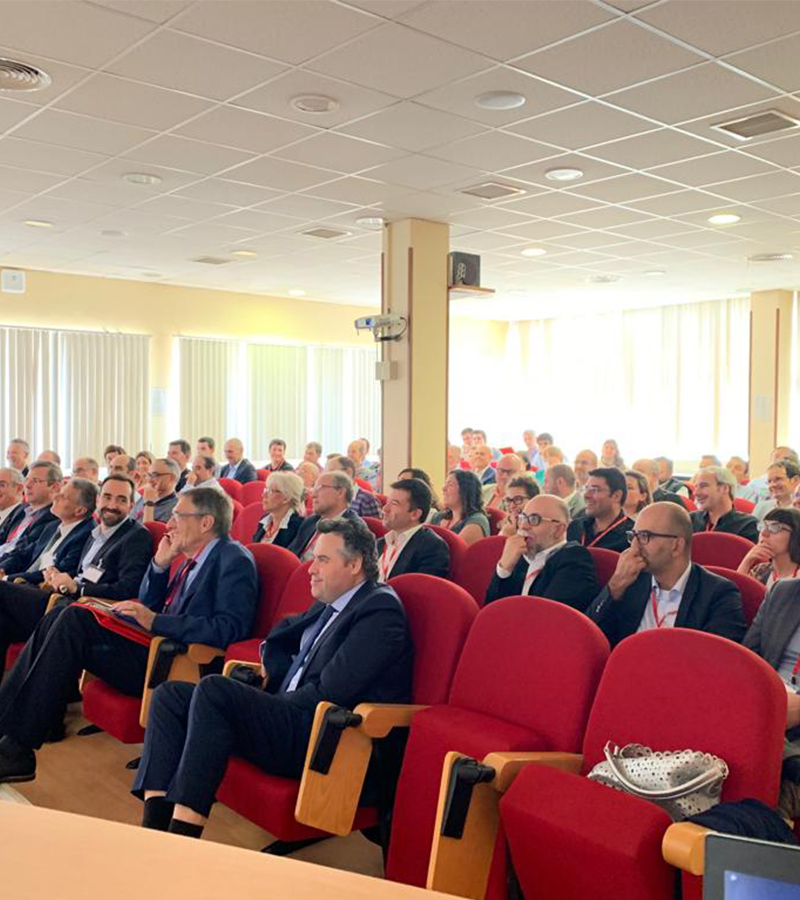
Die Innovation ist einer der besten Verbündeten von Sidenor, sowie eine der strategischen Achsen unserer Aktivität. Sie hat uns zu einer Referenzgruppe im Stahlsektor gemacht.
Die Innovation unterstützt unsere kontinuierliche Verbesserung und hat uns nicht nur dazu geholfen, zu Pionieren in unseren Produkten und Dienstleistungen zu werden, sondern auch dazu, unsere Effizienz, Wettbewerbsfähigkeit, Sicherheit und Achtung der Umwelt zu erhöhen.
Aus diesem Grund wollten wir dieses Jahr unsere Türen öffnen und verschiedene Kunden und Partnerinstitutionen zur Teilnahme einladen, um unsere Vision und die anderer Experten bezüglich der Weiterentwicklungsmöglichkeiten des Stahlgeschäfts im Bereich Innovation zu teilen.
Anlässlich seines ersten Innovationstags hat SIDENOR die Unterstützung anerkannter externer Beobachter erhalten, um die zukünftigen Tendenzen, Chancen und Hindernisse des Spezialstahls sichtbar zu machen. Fünfzig Kunden haben an den technischen Konferenzen teilgenommen und die Gelegenheit gehabt, die neuen Investitionen in die Stahlwerk- und Walzwerkproduktionsanlagen in Basauri zu sehen und die Forschungsteams von SIDENOR F+E zu besuchen.
Nachdem alle Anwesenden von José Antonio Jainaga, CEO von SIDENOR, begrüßt wurden, begann die technische Debatte um das Thema der progressiven Umsetzung der Industrie 4.0 in SIDENOR. Íñigo Legua (CIO) erläuterte die vier Pfeiler des SIDENOR 4.0-Projekts: Smart Factory, Smart Business, technologische Innovation sowie Computer- und Netzsicherheit. Besonderer Erwähnung bedarf das Produktverfolgbarkeit-Projekt zur Identifizierung jeder Stange vom Schmelzprozess bis zur Lieferung an den Kunden, wozu kleine Unternehmen und Start-up-Unternehmen durch die BIND4.0 und BIZKAIA OPEN FUTURE-Programme beitragen.
Im Anschluss an den vorhergehenden Vortrag hielt Herr Professor Bleck – vom renommierten Stahlinstitut der Universität Aachen in Deutschland (IEHK – RWTH Aachen) – zwei Referate über die Anwendung von 4.0 Werkzeugen in der Gestaltung von neuen Stählen sowie über die in der Entwicklung von neuen Schmiedequalitäten erhaltenen Ergebnisse. Im Rahmen einer angenehmen Vorlesung zeigte er, wie die Simulationswerkzeuge, die in der Regel Probleme auf makroskopischer oder mikroskopischer Ebene haben, in einem einzigen System integriert werden können, das die Schwächen von jeder individuellen Analyse überwindet. Konzepte wie ICME (Integrated Computational Materials Engineering), IoP (Internet of Production) oder Digital Shadows ermöglichen die Verarbeitung von Millionen Daten zur Produkt- und Prozessoptimierung in Echtzeit. Die Digitalisierung bietet riesige Möglichkeiten, verlangt aber im Gegenzug eine Änderung der Mentalität, der Verfahren und der Einstellung.
Wenn wir uns auf die Innovation von Stählen im Schmiedesektor begrenzen, erkennen wir drei Haupttendenzen: die Gewichtsverminderung, die Kostenreduzierung und das Ersetzen von strategisch kritischen Rohmaterialen. Zwischen Erfolgsfällen sind die mikrolegierten Stähle, durch deren Anwendung Wärmebehandlungen vermieden werden konnten, die den Prozess verteuern und Energie in großer Menge verbrauchen, das Paradigma. Trotz ihrer unbestreitbaren Vorteile erfordern die mikrolegierten Stähle auch eine hohe technologische Spezialisierung in Anbetracht der Schwierigkeit, die gesamten Prozessvariablen zu kontrollieren, die die Eigenschaften des Endprodukts beeinflussen. Andere vielversprechende Entwicklungen sind die duktilen bainitischen Stähle (HDB), die Stähle mit intermetallischen Präzipitationen, die „gegen Schäden widerstandsfähigen“ Stähle zum Härten und Anlassen und die selbsthärtenden MMS Stähle (Medium Manganese Steels). Diese Konzepte, mit ihren Licht- und Schattenseiten, werden die Zukunft des Spezialstahls in einigen Anwendungen beeinflussen.
Der technische Teil endete mit der Teilnahme eines neuen Redners, Alfredo Fernández-Sisón, Ingenieur im Bereich Getriebe bei SIEMENS GAMESA, der die Herausforderungen erwähnte, vor denen die Windkraftindustrie steht, um die spezielle Leistung zu erhöhen (Drehmoment pro Masseneinheit) und die Zuverlässigkeit der On-Shore sowie Off-Shore Windturbinen zu gewährleisten. Auf graphische Art und Weise zeigte er die Leistungsentwicklung der Windturbinen in den letzten Jahren, von 2 MW bis zu >6 MW in einem Jahrzehnt, was zu einer Steigerung der Belastung des Turms und seines Gewichts und daher zu einer Erhöhung der Drehmomentdichte von 120 Nm/kg bis zu 170 Nm/kg führte, ohne Veränderung in Materialen oder Herstellungstechnologien. Der Kompromiss zwischen Vorsicht und Risiko gelangt an seine Grenzen und es ist nun wichtig, auf dem Weg zur Innovation in neuen Materialen voranzuschreiten und damit die Produktzuverlässigkeit über einen Horizont von zehn bis zwanzig Jahren zu gewährleisten.
Vor dem Mittagessen gab es eine Besichtigung des F+E Labors mit einer Erläuterung der Entwicklungskapazitäten der neuen Stähle von SIDENOR; nach dem Essen erfolgte ein Rundgang durch die Produktionsanlagen von SIDENOR in Basauri einschließlich der neuesten Investitionen in die Stranggussanlage zur Herstellung von 240 mm-Knüppeln, in den runden Vorblock mit einem Durchmesser von 410 mm und in die kontinuierliche Walzstrasse, sowie der Bauarbeiten des neuen Knüppellagers.
Ein kompletter Tag, der der Innovation in Spezialstählen gewidmet wurde – es war der Erste, sollte aber, angesichts der guten vermittelten Eindrücke und der positiven Reaktionen von allen Anwesenden, nicht der Letzte sein. Der erste Schritt auf einem Weg, den SIDENOR Hand in Hand mit seinen Kunden und seinen Arbeitern einschlagen wird.