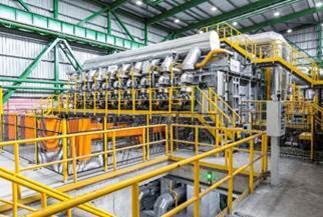
The revamping of Sidenor’s new rolling mill aim at ensuring the effectiveness of rolling processes, increasing their control, quality and stability, while keeping the door open to future productivity increases. For this purpose, and based on an improved cross-section of the billet (240×240) as well as the removal of the previous, obsolete roll stands, we intend to reach a better reduction in our entire range of products, thus obtaining improved internal quality for our customers, as well as improved surface quality. The whole restructuring, including installations, engineering and automation as well as the complete mounting and activation of the mill, has been performed by the German group SMS. The purchase order was concluded in October 2016 and included a very demanding execution deadline; the mounting was performed over August and September and it came into operation in October 2017. As part of the update, the former furnace has been replaced by a brand new cooled walking beam furnace, including the entire equipment for the transport of the billets when entering or leaving the furnace. The heating of billets occurs by means of highly efficient burners, reducing the quantity of particles and NOx emitted by Sidenor in the environment.
The whole process is regulated by means of a software which heats the bars in a controlled and homogeneous manner, according to pre-established parameters, enabling the immediate detection and notification of any abnormal working condition and ensuring the stability of the heating process for all elements to be laminated.
Its modular capacity enables a productivity increase from its current level (85 T/h) to 130T/h, if necessary, in the future. The exit of the furnace is equipped with a husking unit with high pressure water, which eliminates the remaining mill scale from the billet surface, ensuring the elimination of scaling in the hot material.
In addition, the former open slabbing mill has been replaced by a complete continuous slabbing mill composed of 6 stands.
A new cutting shear for heads, tails and short bar optimization enables the elimination of non-valid remaining parts before they are produced, leading to cost reductions and ensuring that they cannot be delivered to the customer. Two new stands have been added to the existing rolling train, enabling adequate reduction ratios, improving the central compactness of the product and materialising the possibility of laminating our whole range of round bars from 20 up to 120mm in the future.
Finally, thanks to a new bar shear, we are able to cut multiple bars while respecting the lengths required by the customer, thus optimizing costs incurred by inadequate cuts and materialising the possibility, in the future, of cutting bigger or smaller sections compared with the current dimensions, according to customer needs.
With the restructuring, Sidenor aims at becoming one of the leading providers of special steel rolled bars in all dimensions of our range. At the moment, Sidenor Basauri is focused on ensuring quality processes in the production of high-quality steel bars of 29 to 100mm diameter, including steels with high, medium and low carbon level, alloyed steel, micro-alloyed steel, tool steel, bearings, stainless steel as well as free-cutting steel, intended for the car sector as well as the oil and gas industry.