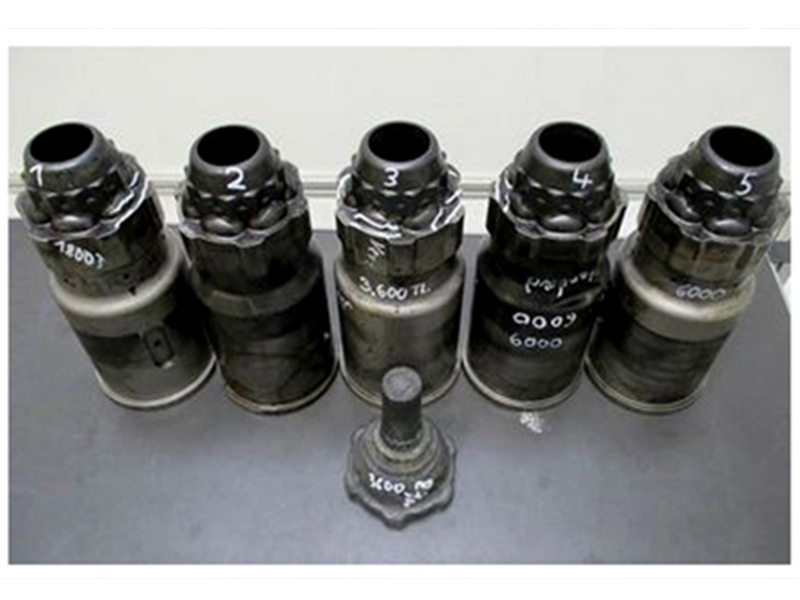
Sidenor presents the RFCS Project TOOLSTEEL: new steels that increase and improve the life of hot forging tools
To increase the life of the tools is a big challenge for the hot forging companies. The extreme service conditions limit the correct performance to about 15.000 forged parts. Considered the high production rate of the automatic presses, this means that the service time of the tools is around 3 hours, and consequently requiring to stop the production to change them. Choosing the correct alloy to manufacture the tools is a key factor of the process to avoid early failures, and to optimize the effective time of production.
Sidenor presents today the conclusions after collaborating in the European RFCS Project TOOLSTEEL, finished in june 2017, coordinated by Tecnalia, in wich Sidenor R&D has worked together with Volkswagen AG and the steelmaker Schmiedewerke Gröditz in the project development.
Starting from the H10 steel, a new alloy has been developed, whose performance has been tested in industrial trials, in order to improve the hot forging tools’ life in hot forging hatebour equipment.
The presentations will be emitted today in an online webinar. They will explain the Project development: the analysis of the failure mechanism of the forging punches, how new different alloys have been designed and produced at a laboratory scale to choose the most promising one, and the trials at an industrial level with punches made of the new tool steel.
The new alloy has already been used in several forging campaigns with good results.
Get registered to the webinar to learn all the details of the project!