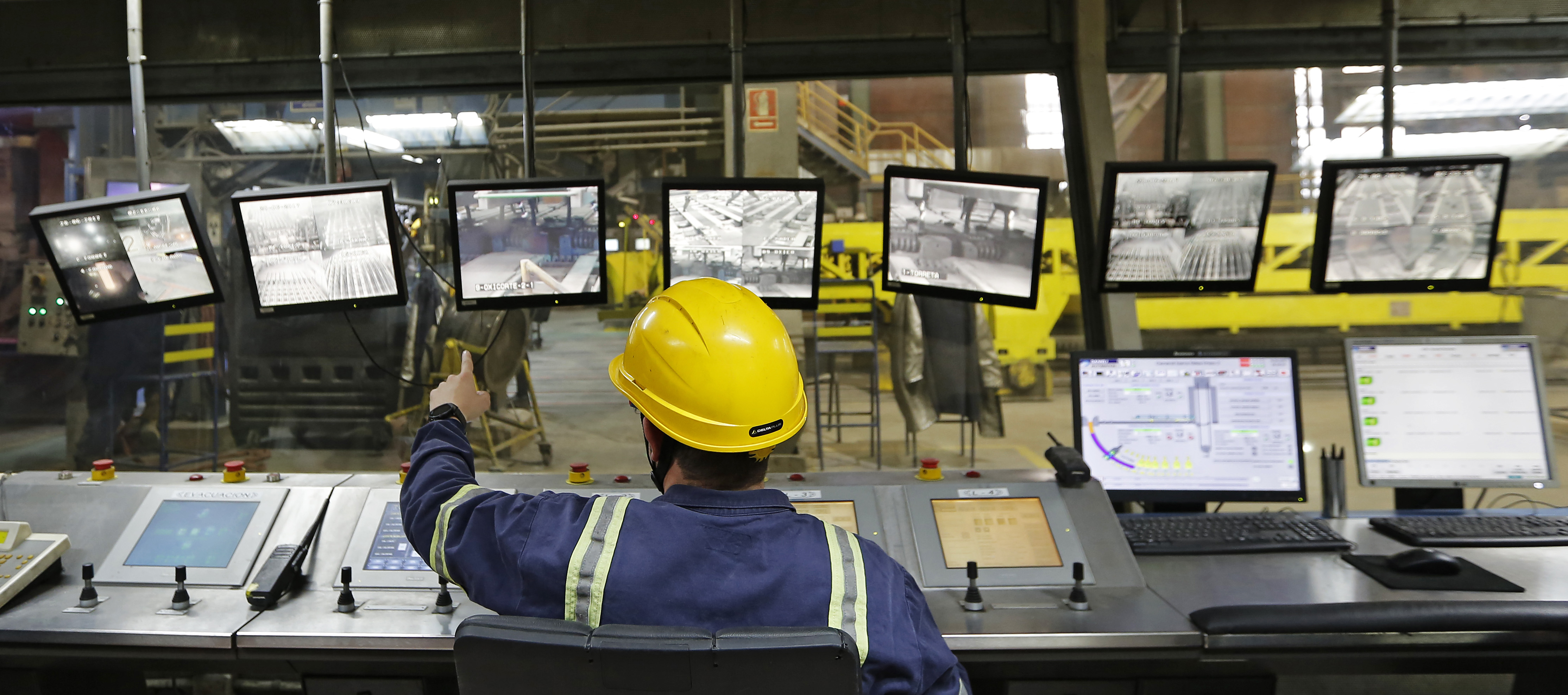
COCOP is a digitization project focussed on the development of an optimisation tool for complex processes such as those in the steel sector. The COCOP project aims at achieving monitoring and control at factory level by coordinating the optimization of the various processes and by using integrated predictive models with the local control systems.
In the steel use case, the aim was to develop a “digital twin” in order to reduce the number of surface defects in the final micro-alloyed steel product, ensuring a good performance of the production sub-processes associated with the occurrence of defects (secondary metallurgy (SM), continuous casting (CC) and hot Rolling (HR)).
4 data-based models were developed (SteelSM, SteelCC, SteelHR and SteelDefects), whereby the following steps were taken:
Descriptive data analysis for the purpose of understanding the process,
Data cleansing and detection of outliers,
Regression model in order to predict the target variable. Various techniques were tested, such as “neural networks, random forest and gradient boosting”.
Model performance assessment by means of a cross-validation approach.
This project has been financed within the framework of the European Union research and innovation HORIZON 2020 programme; the consortium partners include renowned entities at European level in the university area as well as among research centres.
Among the achieved objectives, it is worth highlighting the development of monitoring and alarm online tools for secondary metallurgy as well as continuous casting processes and the development of optimisation tools aiming at identifying the optimal values of parameters which impact secondary metallurgy, continuous casting and rolling processes, in order to achieve a good performance of each sub-process and minimise the number of defects in the final product.
These results will entail the further reduction of the finished product’s rejection rate, the conditioning rates and the defect share in continuous casting.
The industrial trials have demonstrated the technical feasibility of the developments contemplated in the project, which will besides facilitate decision making in case of potential contingencies during the manufacturing process.
All information regarding the project is available on its webpage https:// www.cocop-spire.eu/ where various materials can be downloaded, including a technical blog in which all partners participate monthly.