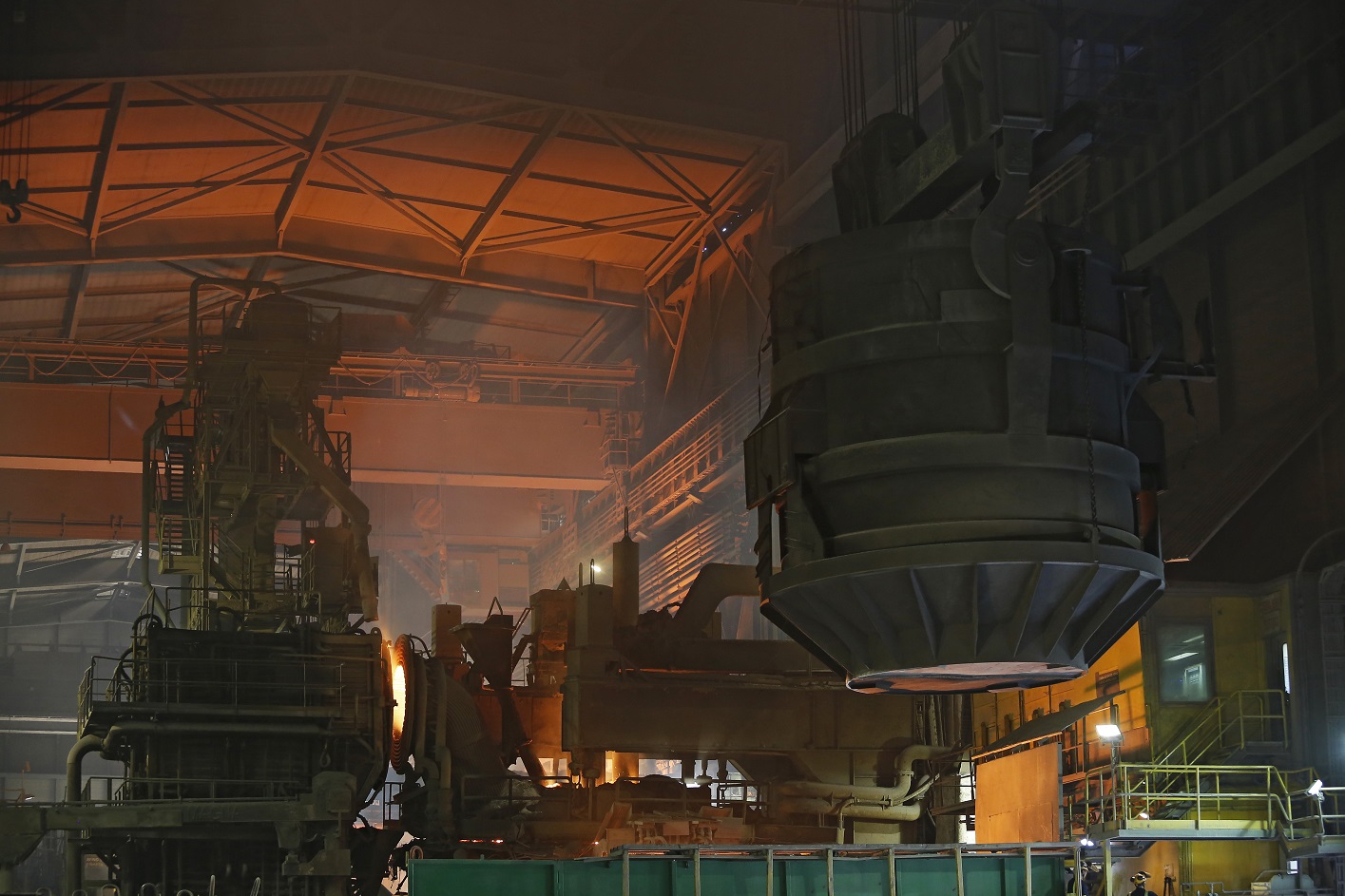
Within the framework of its commitment to circular economy, Sidenor is carrying out various projects aiming at improving the quality of the steel it produces, while reducing raw material and energy consumption. These projects include new measurement parameters so as to further facilitate the setting of thermal processes and improve the control of operating procedures.
These operating advantages translate into a further optimization, thus avoiding processing losses; accordingly, these projects aim at improving productivity and steel quality scores. The reduction of processing losses and the increased process efficiency entail the reduction of electrical energy as well as raw material consumption.
Besides, Sidenor is also carrying out other circular economy projects, mainly on the valorisation and utilisation of by-products obtained during the metallurgy process.
Through its Environmental Department – that is, Ihobe –, the Basque government has approved, within the framework of the 2019 eco-innovation and ecodesign programme for circular economy, the aid in favour of various business plans; Sidenor participates in three of these projects, as the leader of two (Stirladle and Termoslag) and a partner in the third (Tracex).
The programme aims at reaching the environmental and technical-economic viability of innovative solutions that are able to improve the competitiveness and differentiation of Basque companies in the medium term, while fostering eco-innovation and circular economy. The three projects mentioned above comply with these characteristics.
In the following, we will share some specific technical features of the two projects led by Sidenor, as well as the environmental benefits entailed by each of them.
The STIRLADLE project is entitled (“Development of a system for the online control of steel stirring in the ladle.”)
The project mainly aims at developing and implementing a control system in order to accurately characterise steel stirring in the ladle and analyse the information on stirring obtained from the implemented smart sensors. The solution proposed by SIDENOR implies the following specific objectives:
- Improving productivity thanks to process optimisation and control by means of new process variables monitoring systems,
- Improving steel quality scores,
- Reducing billet scrapping due to possible quality defects, thus improving energy efficiency and the resources used to obtain the semi-product.
Specifically, we will work with the measurements of vibrations caused by the movement of the steel in the ladle, which is generated by the gas flow through a porous cap.
Thanks to this project, we will obtain a more efficient and environmentally friendly secondary metallurgy process by means of electrical energy consumption reduction.
The TERMOSLAG project (“Development of a sensor for the online control of the passing of scrap to dumping in the EAF”) is in line with the circular economy demonstration line.
The main objective is to achieve the online control of slag transit during liquid steel dumping in the electric arc furnace (EAF) by developing and implementing a thermographic camera, thus preventing the slag from passing into the ladle. The expected results are the following:
- Reducing the quantity of slag that might pass into steel by 10%.
- Reducing raw material and energy consumption by optimising as much as possible the secondary metallurgy process.
- Improving steel quality, avoiding the recovery of elements such as the passing of slag into steel.
The measurement data will be automatically collected and stored in a data processing software and the impact of the passing of slag on variables such as the rate of desulphurisation, castability or wear of the refractory material will be studied.
Thanks to the development of this project, we will achieve an increased manufacturing efficiency, using natural resources in a responsible and environmentally friendly way, by minimizing the passing of slag to secondary metallurgy which might result in higher energy and raw material costs.