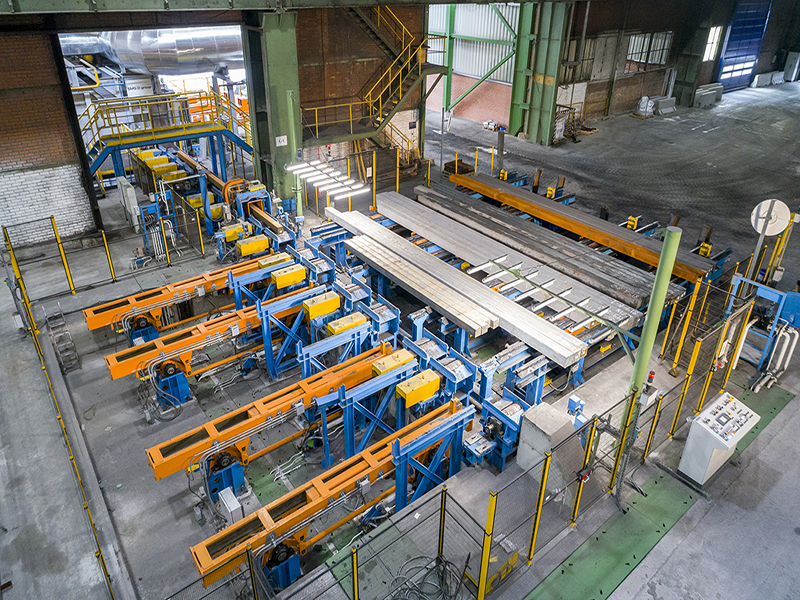
In a business such as ours, where our special steels are mainly intended for demanding sectors such as the car industry, ensuring a perfect product traceability has become not only a requirement, but also an inner principle by means of which we know exactly where and when each of our references are at the various stages of the production process.
Within the rolling process, product traceability starts with the introduction into the heating furnace.
By means of continuous data transmission from our Departmental System (MES) with the new machine vision label reading devices of Cognex®, each of the billets is checked before its introduction into the furnace. The operation is “simple”: once the billets are placed in the last position of the loading table, and after measuring their length via laser, they are transferred to a scale which weights them in order to start the internal calculation of the cutting parameters of the various shears (the so-called “Cutting Strategy”). Precisely at this moment, when the billet is being weighted, appears the new machine vision reading system.
The new reading system consists in 4 cameras, 2 on each side of the loader, which read the identification label of each billet before it enters the furnace. The reason for installing 2 cameras on each side is due to the variety of the billet sizes, which go from 4,000m to 9,835mm. Each camera on each side is optically adjusted to a measuring range, so as to ensure that we can obtain an adequate vision of each billet length included in the acceptable range.
The system consists in additional lighting from above in order to ensure that the best definition can be obtained in each situation. Once the new machine vision devices have read the label, and provided all is ok, the billet is transferred to the roller track for entering the furnace and following its process. In order to provide the furnace operator with the highest quantity of data, the system has a screen which shows the best picture made by each camera of each billet.
In case of nonconformity, the HMI of the furnace informs the furnace operator acoustically and visually that the label does not match the assigned casting, and it is sent to the rejection table, without entering the process.
The new label reading devices allow us to read 100% of the billets introduced in the furnace, which is essential for ensuring the traceability of the product for our internal as well as external customer. Machine vision systems, big data analysis, industry 4.0, etc., are no longer futuristic concepts: they have become reality, our reality.